Advantages of Non-Metallic Sprockets
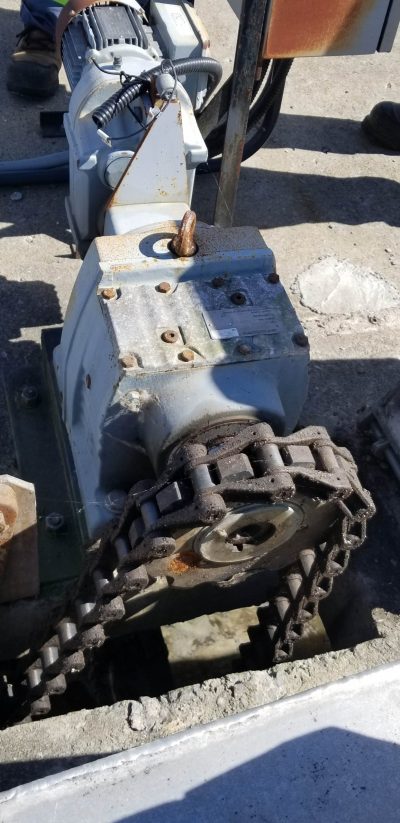
Advantages of Non-Metallic Sprockets
Non-metallic sprockets have gained popularity in recent years as an alternative to traditional metal sprockets due to several advantages they offer. One significant benefit is their ability to reduce noise levels. Metal sprockets can generate considerable noise, particularly in high-speed applications, but non-metallic sprockets are quieter due to their inherent dampening properties. This is especially important in applications where noise reduction is critical.
Non-metallic sprockets are also typically lighter than metal sprockets, which can be essential in weight-sensitive applications. The lighter weight of non-metallic sprockets can reduce the load on other system components, like bearings, which can lead to longer service life and reduced maintenance costs.
Another advantage of non-metallic sprockets is their improved corrosion resistance compared to metal sprockets, which can be prone to corrosion when exposed to moisture or other corrosive environments. Non-metallic sprockets are not susceptible to corrosion and thus ideal for such environments.
Non-metallic sprockets also offer improved wear resistance over metal sprockets, making them more durable in harsh or abrasive environments. They offer longer service life and reduced maintenance costs in these applications.
Finally, non-metallic sprockets can be a cost-effective alternative to metal sprockets, especially in lower-load or lower-speed applications. Additionally, they may be easier to manufacture or repair than metal sprockets, as well as reduce the wear on the chain leading to cost savings.
Overall, non-metallic sprockets have become increasingly popular in recent years due to their ability to reduce noise levels, weight, and corrosion, as well as improve wear resistance and cost-effectiveness. As materials science and manufacturing technology continue to advance, it is likely that non-metallic sprockets will continue to gain popularity as a viable alternative to traditional metal sprockets.
Putting Thordon Bearings to Work in the Wastewater Industry
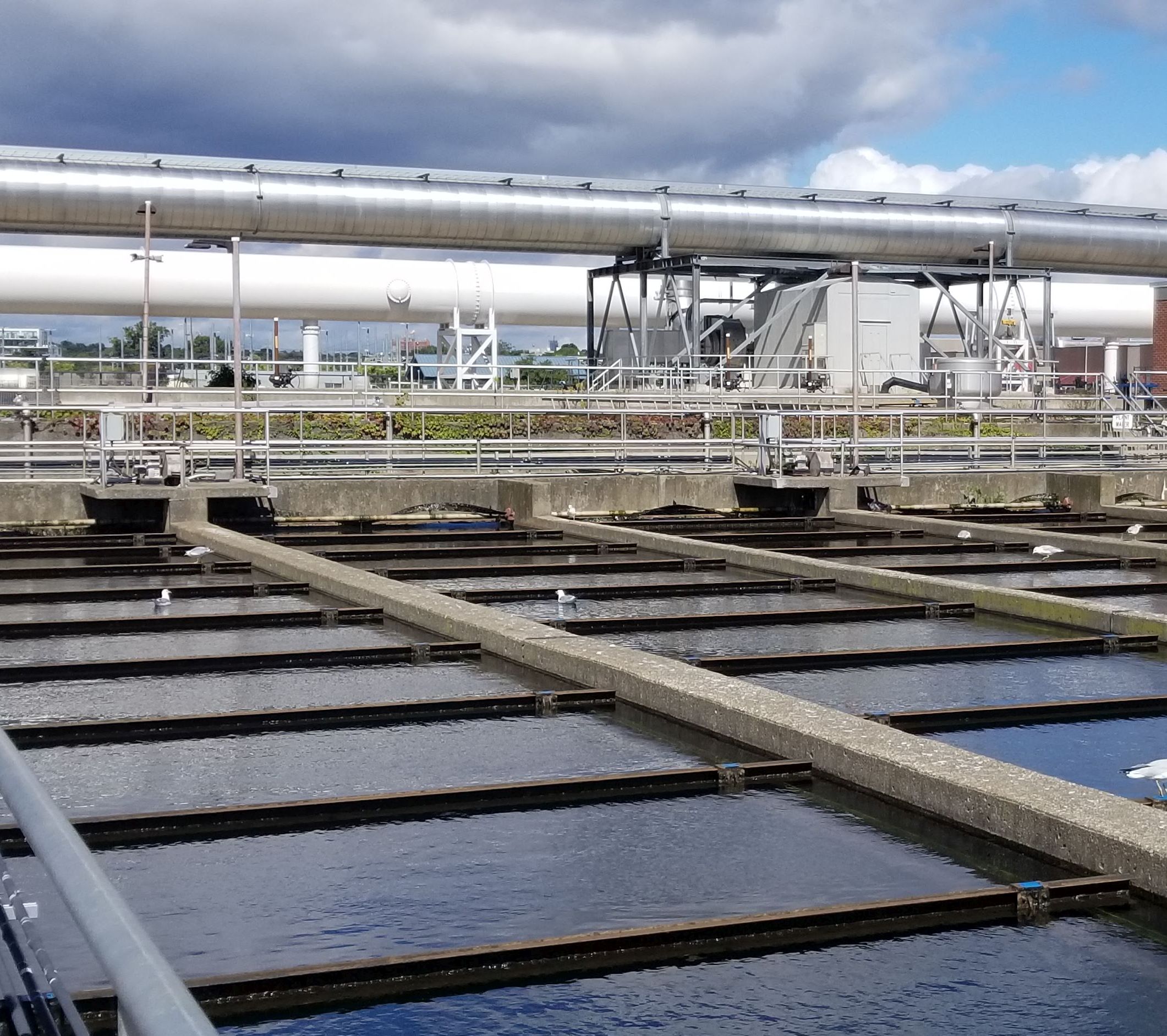
Wastewater Treatment Case Study
The Expensive Problem: The Scraper Cog Wheel Sprockets (which are important components of the sludge removal system) in a wastewater treatment plant were failing due to excessive flexing. The original sprocket design utilized a plastic material with a brass sleeve inserted at the center of the hub for power transmission. Unfortunately, as the sprocket rotated, the plastic body would flex, leading to the gradual loosening and detachment of the brass sleeve. Consequently, the sprocket would cease to operate effectively.
Thordon’s Efficient, Cost-Effective Solution: Millstream proposed to make the sprocket using Thordon Regular material which possesses superior properties including high strength and self lubrication. This eliminated the need for a metal sleeve which allowed the sprocket to run freely on the axle in case of breakage of the drive pin due to an overload on the chain. To match the sprocket’s profile accurately, the Millstream team had the original sprocket 3D scanned and modeled using CAD software. The sprockets were then machined with some design improvements. A Shear pin through the hub connects the sprocket to the axle for power transmission. If there is an overload condition on the chain, the shear pin will break allowing the sprocket to move freely around the hub without transmitting power or damaging the equipment.
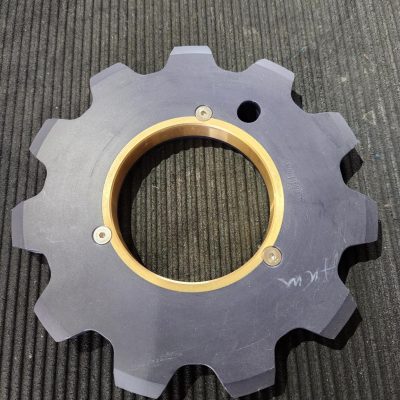
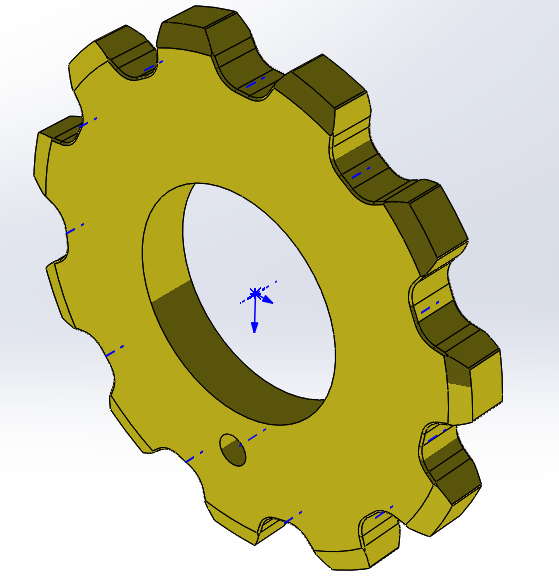
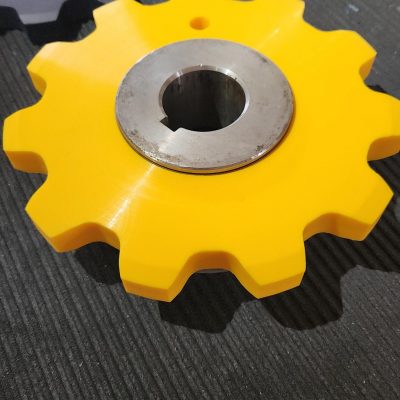
Original Sprocket with Brass Sleeve
3D CAD Model
New Thordon Regular Sprocket
Do you have expensive challenges with your bearings and need a creative, cost-effective solution? Allow Millstream Engineering’s team of specialists to lead your group to a successful, economical solution. Contact us today.