(Not) Cracking Under Pressure: Unveiling Mechanical and Thermal Failures in Non-Metallic Bearings
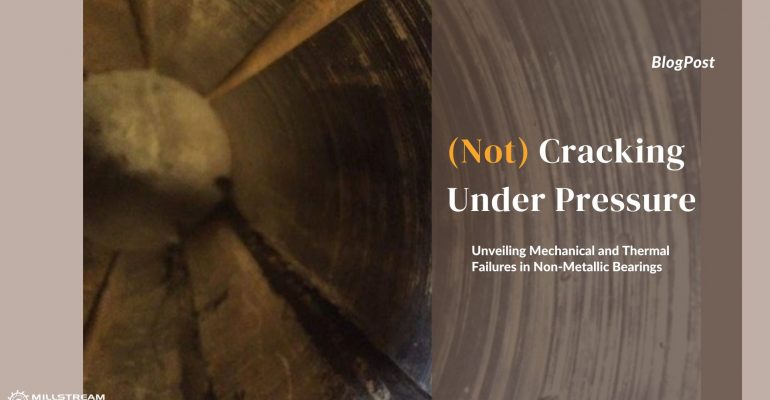
(Not) Cracking Under Pressure: Unveiling Mechanical and Thermal Failures in Non-Metallic Bearings
Mechanical Failure Modes
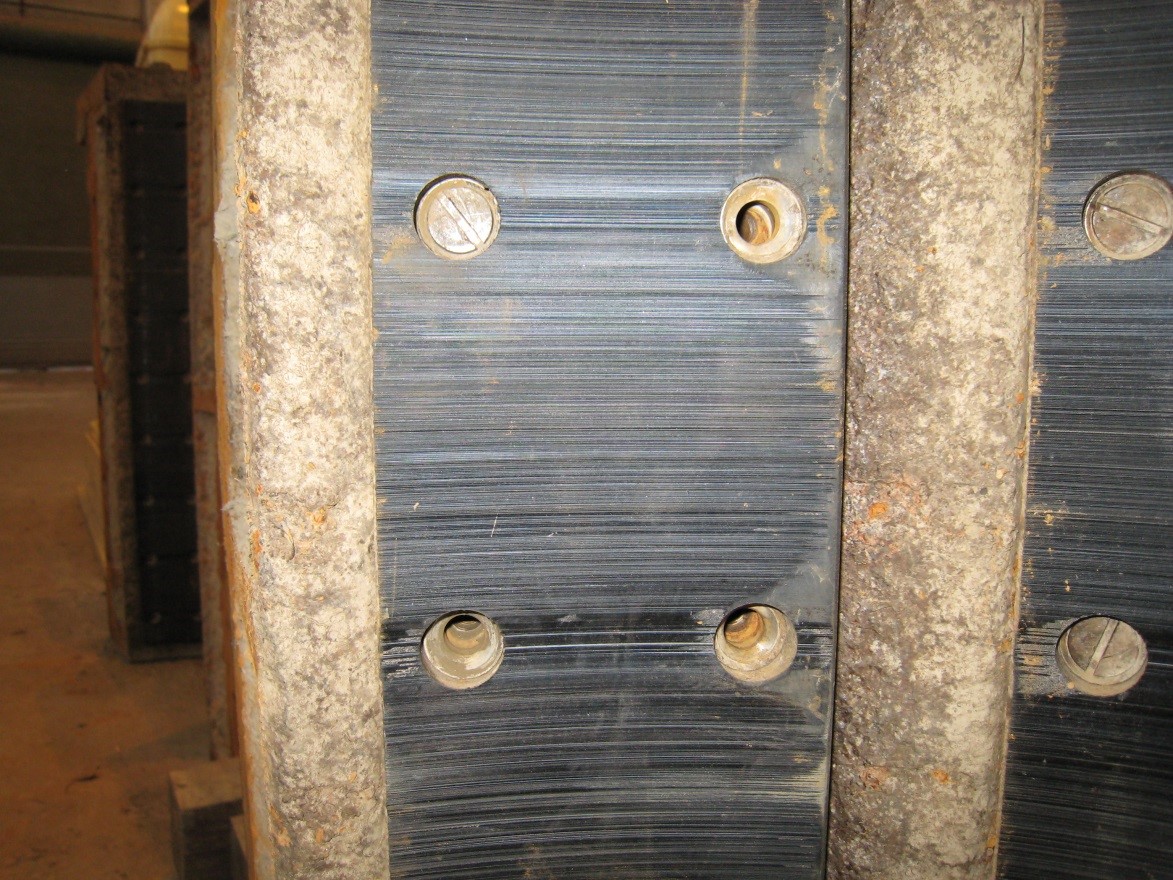
Wear & Abrasion
How To Reduce Wear & Abrasion
Creep and Deformation Under Load
How to Limit Creep Deformation
Impact and Fatigue Failures
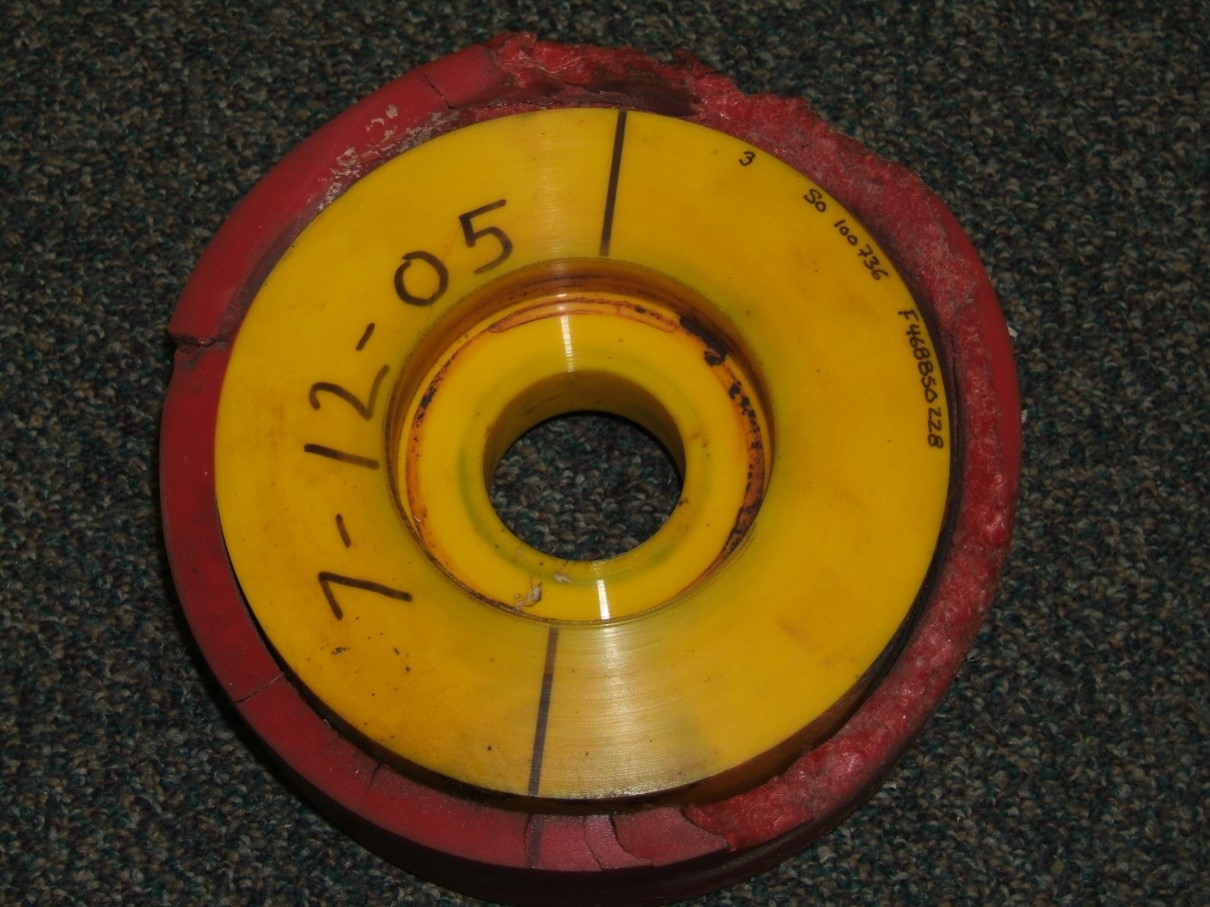
Strategies to Minimize Impact & Fatigue Failures:
Thermal Failure Modes
Thermal Degradation
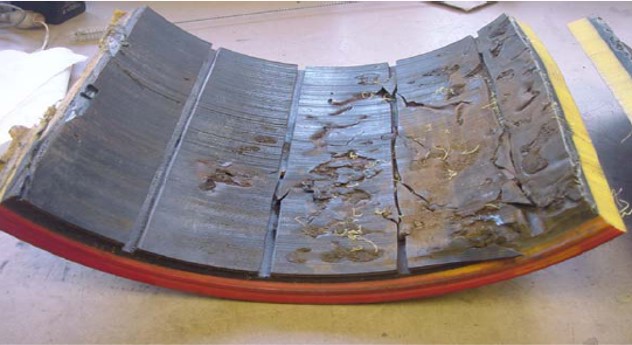
How to Limit Thermal Degradation
Thermal Expansion and Contraction
Mitigation of Thermal Effects
Thermal Fatigue
Reducing Thermal Fatigue Effects
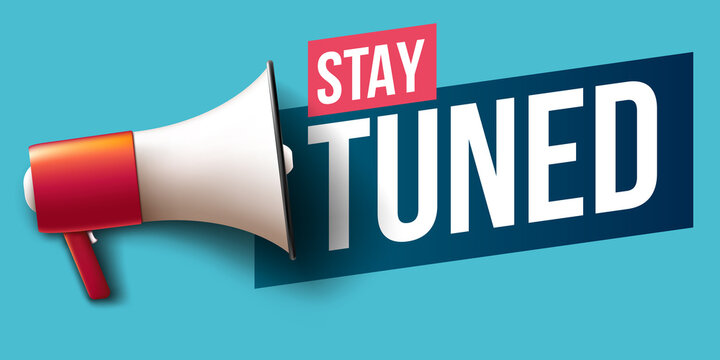