The Mechanics of Centrifugal Casting: A Deep Dive into Industrial Ingenuity
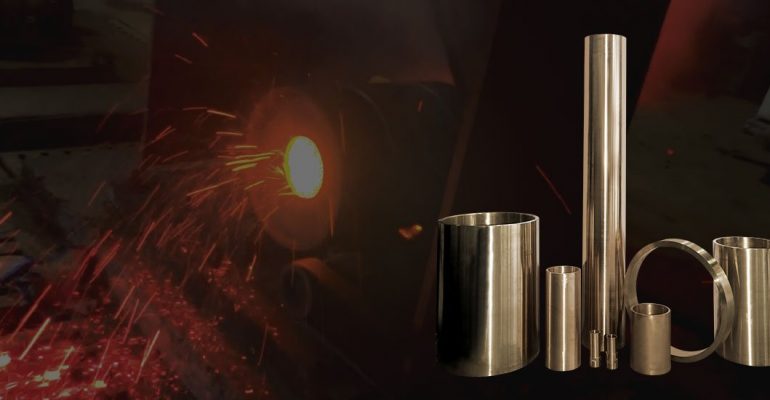
The Mechanics of Centrifugal Casting: A Deep Dive into Industrial Ingenuity
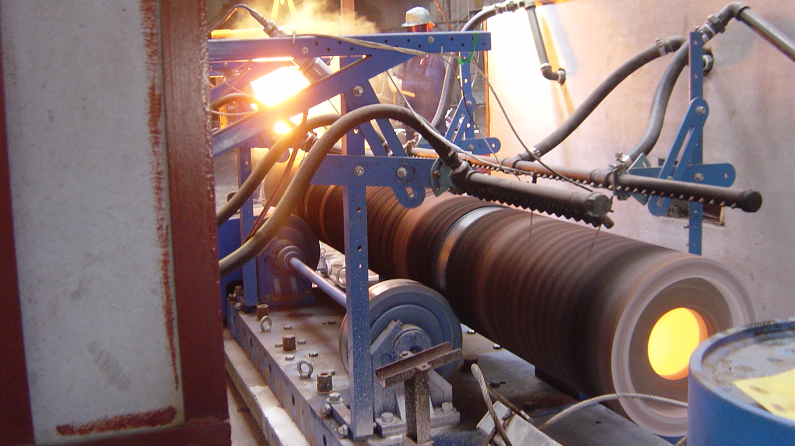
Rotational Molding
The process begins with a cylindrical mold/die that rotates around its axis at high speeds (can be more than 1000 rpm!). This mold can be horizontal, vertical, or inclined, depending on the desired product.
Pouring Molten Metal
As the mold spins, molten metal is poured into it. The centrifugal force generated by the rotation causes the metal to spread uniformly along the mold's inner surface, with the solidification taking place from the outside to inside.
Centrifugal Force at Play
The key aspect of this process is the use of centrifugal force, which drives heavier impurities (usually oxides and other inclusions) inward towards the center. This part of the metal doesn't solidify in the mold and is later removed, ensuring the final product is of high purity and free from defects.
Cooling and Solidification
The metal cools and solidifies against the mold walls, forming the desired shape. The centrifugal process creates a very tight and defined grain structure due to the directional solidification of molten metal under high pressure. The castings produced by this process are free from surface / sub-surface defects & have almost no porosity. Once cooled, the component is removed from the mold.