Tech Tips – Surviving the Elements: Mitigating Environmental Failures in Non-Metallic Self-Lubricating Bearings
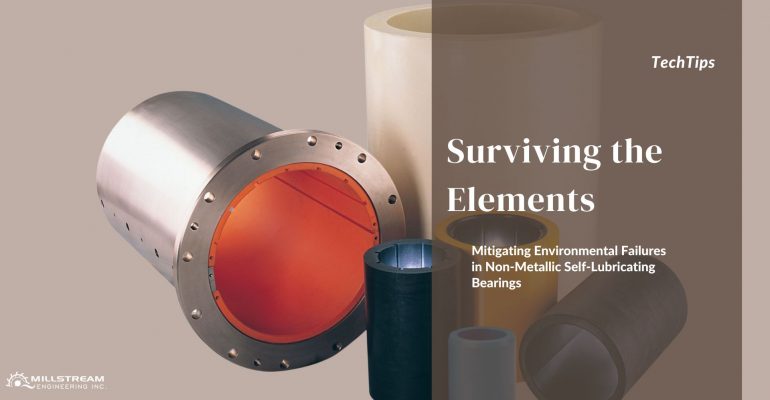
Tech Tips – Surviving the Elements: Mitigating Environmental Failures in Non-Metallic Self-Lubricating Bearings
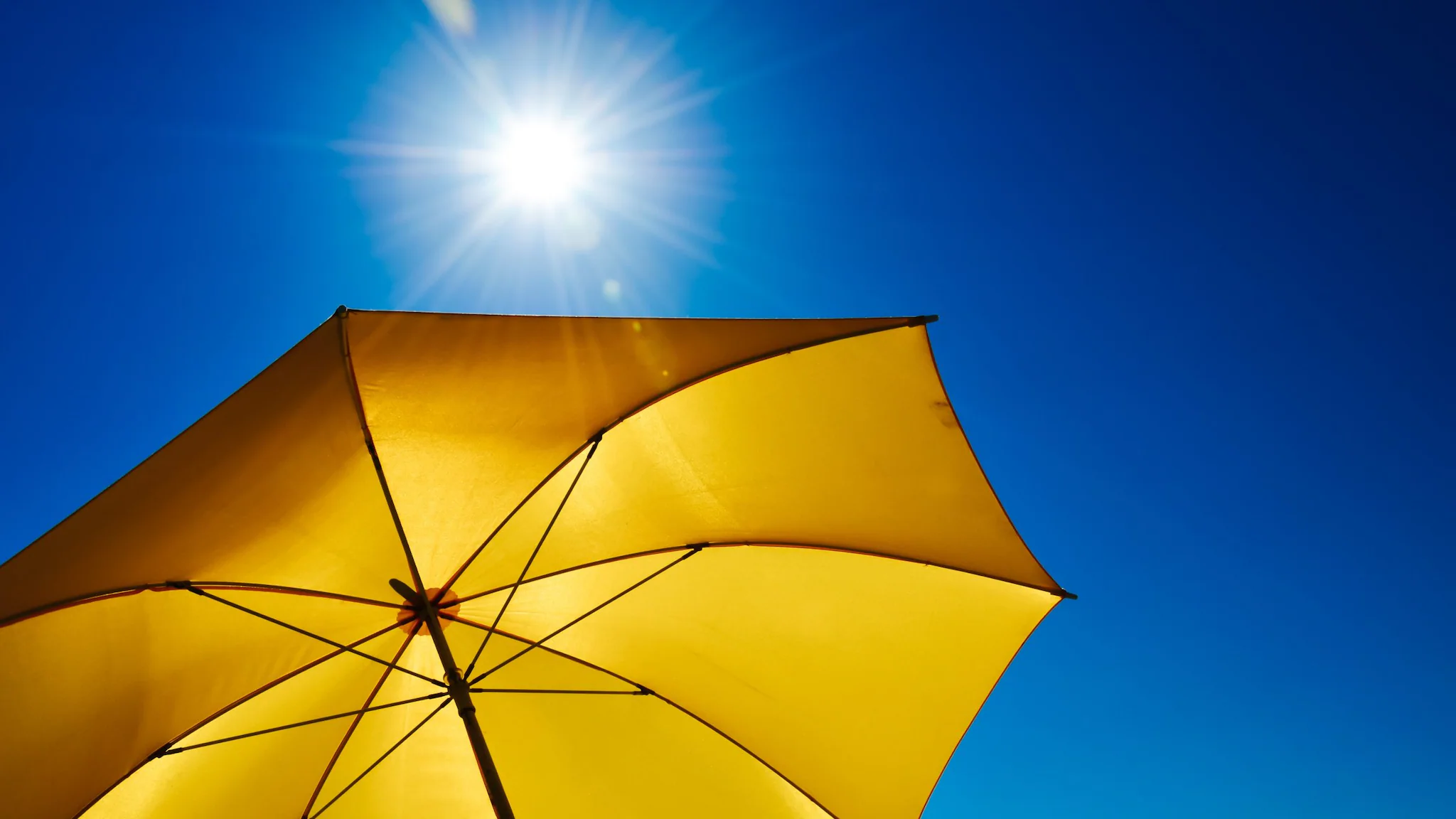
Have you ever thought,
How Do Environmental Factors Like Chemicals, UV Exposure, and Moisture Impact the Performance of Non-Metallic Self-Lubricating Bearings?
Environmental Failure Modes

Chemical Degradation and Corrosion
Mitigation Strategies
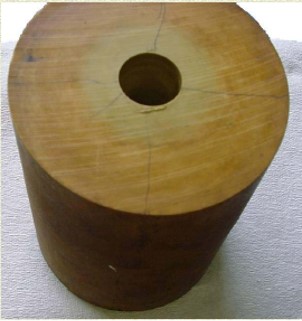
UV Degradation and Weathering Effects
Mitigation Strategies
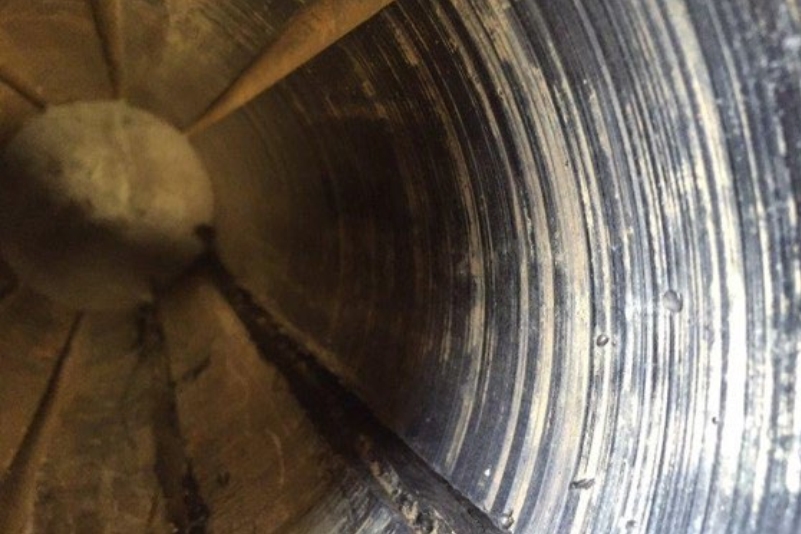
Moisture-Related Failures
Mitigation Strategies
Future Trends and Innovations
Understanding and mitigating environmental failure modes are crucial for the reliable performance of non-metallic self-lubricating bearings. By selecting the right materials, implementing protective measures, and leveraging advancements in technology, these bearings can thrive in harsh environments. This blog series has explored the comprehensive testing methods, mechanical and thermal failure modes, and environmental challenges faced by these materials, providing a holistic view of ensuring their reliability.
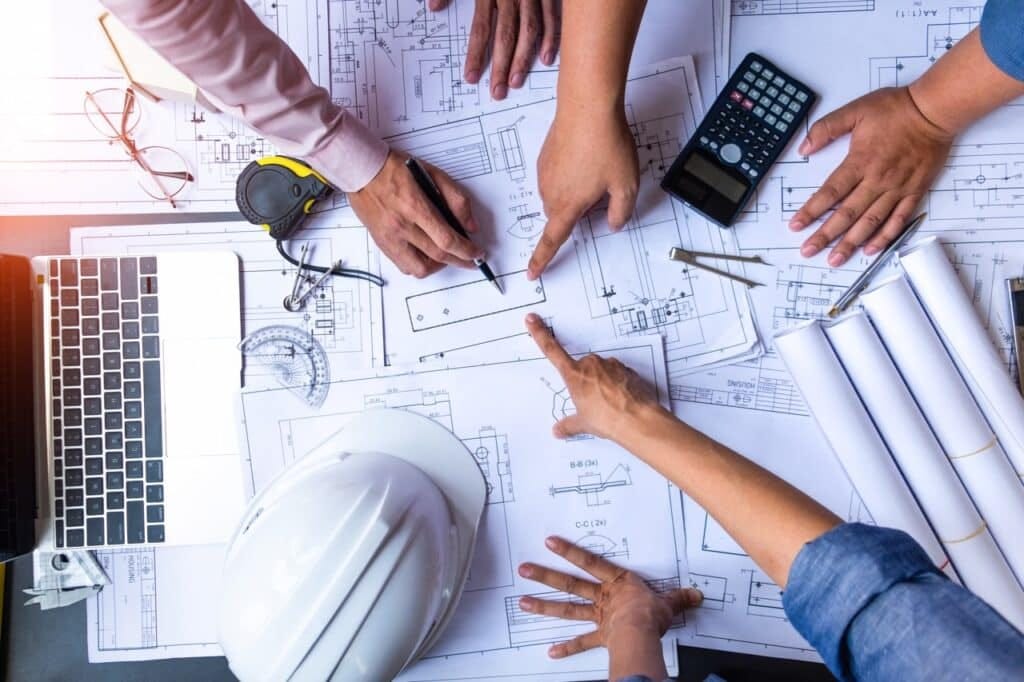