Thordon Bearings: A Proven Solution for the Demanding Mining Industry
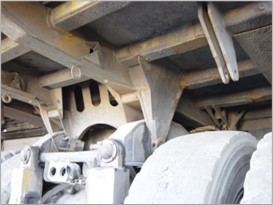
Thordon Bearings: A Proven Solution for the Demanding Mining Industry
Mining is arguably one of the most difficult operating environments in any industry, with the most punishing wear on equipment and its components. Greased bronze bushings, which have traditionally been used in mining equipment, require regular maintenance because they are exposed to dirty, humid, cold, abrasive, and wet conditions. Enter the hard-working, continuously out-performing Thordon Bearings, a thoroughly tested and proven solution.
In mining applications that involve abrasive dust, dirt, grit and debris, Thordon materials like ThorPlas-Blue and Thordon Elastomers eliminate the need for grease and repeatedly bounce back from shock and impact loads. Thordon’s grease free bushings are used in a variety of mining equipment applications, including crushers and feeders, skip pivots, centrifuges, chaseblocks, and truck stabilizers.
Thordon bearings are a tried-and-true solution that offer a diverse range of polymer bearings that consistently outperform traditional greased bushings while significantly lowering associated operating and labour costs. Thordon bearings substantially reduce downtime by maintaining stability through heavy shocks with less wear.
Putting Thordon Bearings to Work in the Mining Industry
Mining Case Study Number 1: Truck Stabilizer
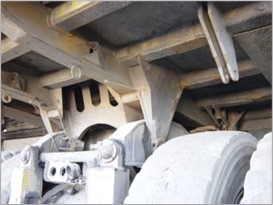
The Expensive Problem: Large bronze bushings for a 100-ton mining truck stabilizer (steady axle) were having to be replaced after only 2500 hours of use. Next were tried nylon bushings which were somewhat of an improvement over the bronze bushings by lasting 7000 hours.
Thordon’s Efficient, Cost-Effective Mining Solution: Still not satisfied with this performance, the engineers turned to self-lubricating ThorPlas-Blue. This Thordon material is easy to custom make and machine the large sized bushings needed (348 mm (313.7”) x 327.5 mm (12.9”) x 101.6mm (4”)). Most importantly, these bushings currently continue to operate without issues for over 13 000 hours with no need for expensive downtime or maintenance.
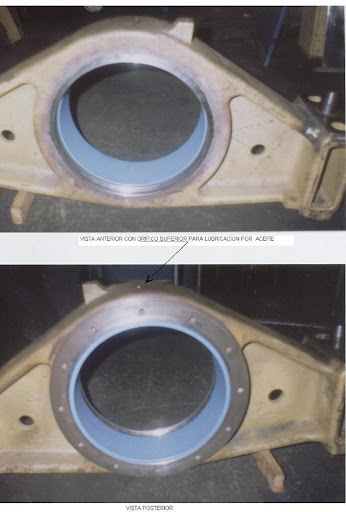
Mining Case Study Number 2: Wheel Loader Bearings
The Expensive Problem: A Wheel Loader’s solid carbon steel bearings required constant lubrication. Grease combines with dirt, water, or both, causing bearings to wear out much faster. Bearings are difficult to remove and reinstall, resulting in high maintenance costs.
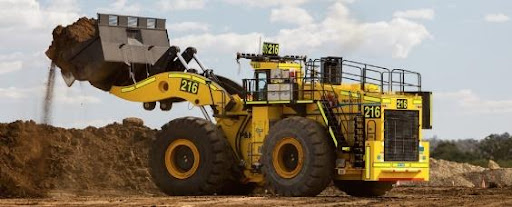
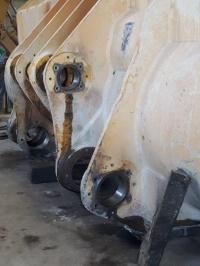
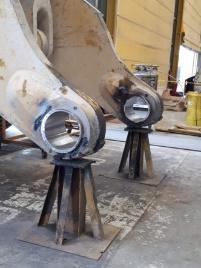
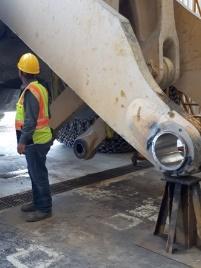
Thordon’s Efficient, Cost-Effective Mining Solution: ThorPlas-Blue self-lubricating bearings eliminate the need for grease, reducing overall ownership costs. As a result, the bearings’ wear life was extended, and downtime was greatly reduced. New ThorPlas-Blue bearings are much easier to remove and reinstall further reducing maintenance costs.
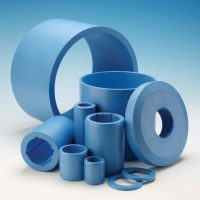
Do you have expensive challenges with your bearings and need a creative, cost-effective solution? Allow Millstream Engineering’s team of specialists to lead your group to a successful, economical solution. Contact us today.