Hydro Case Study – Upgrade Greased Babbitt To Water
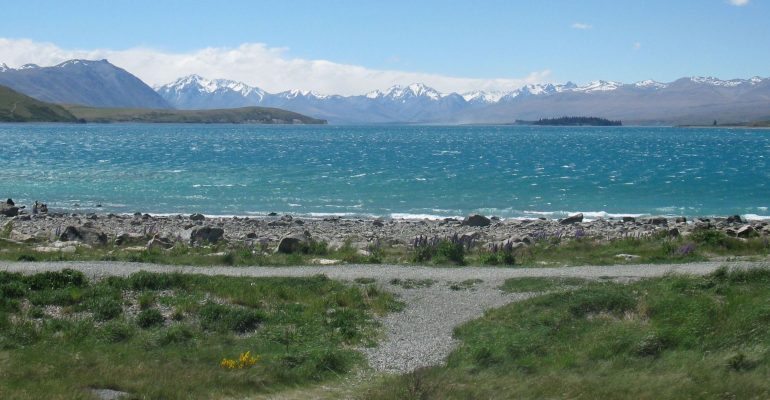
Hydro Case Study – Upgrade Greased Babbitt To Water
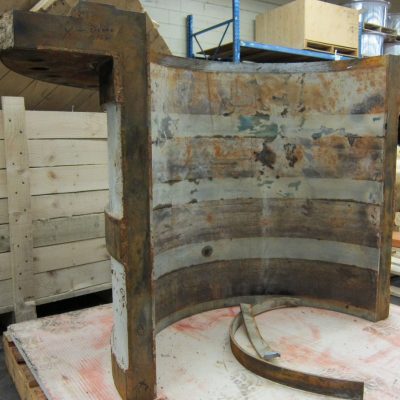
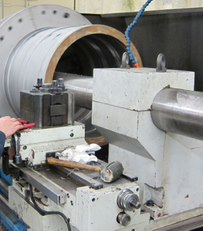
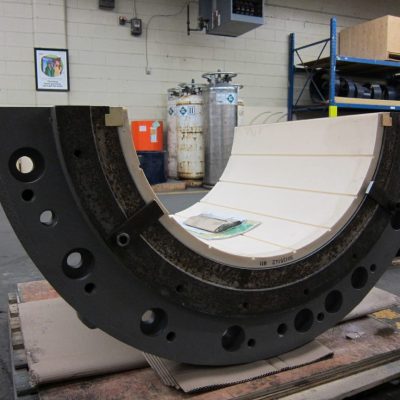
ORIGINAL BABBITT BEARING LINING IN FLANGED HOUSING
MACHINING THE HOUSING
NEW THORDON SXL BEARING
In order to control the quality and accuracy of the modifications to be done, the customer shipped the original bearing housing to the Thordon factory for retrofitting, including machining out the babbitt layer and modifying the housing to accept a new split bearing using the Thordon SXL elastomer. One unique feature of the design was the use of bronze “keeper bars” to retain the split-bearing shells without the use of any adhesives or additional fasteners. This also allows for easier replacement of the bearing shells in the future.
The existing shaft seal assembly was maintained, the original grease delivery system was removed, and a conditioned water supply was connected to provide cooling & lubrication. The new bearing was re-installed in the turbine and is now providing the customer with the trouble-free, and grease-free operation – ensuring that the downstream river water stays just as clean as it is coming into the plant! For several years of operation, the customer closely monitored the turbine vibration in the lower bearing and although they have observed some seasonal trends due to variations in river water temperature, it is in line with predictions provided by Thordon Engineering.
Thordon SXL is made in Canada, with a proven track record in Hydro applications for over 20 years. The Thordon SXL elastomer offers a low coefficient of friction, superior wear performance, and minimal maintenance requirements by entirely eliminating the need for grease or oil lubrication.