Hydro Tech Tip – Greaseless Bushings for Servomotors
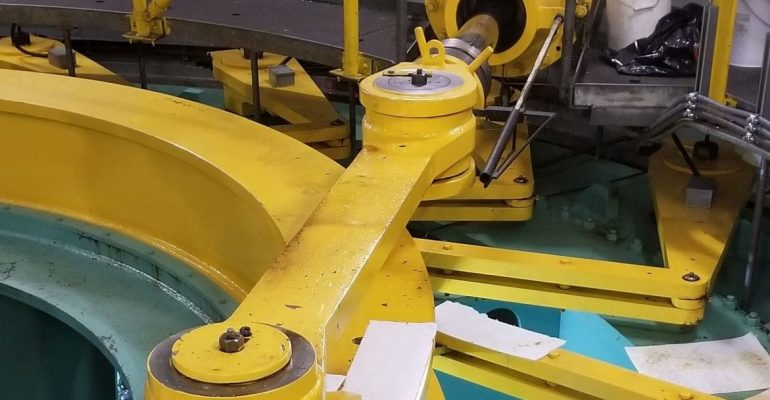
Hydro Tech Tip – Greaseless Bushings for Servomotors
Understanding the Function of Servomotors
Hydropower plants typically rely on servomotors (large hydraulic pistons) to deliver the motivating force to the operating mechanism for opening or closing the wicket gates. The servomotor movement is controlled by the speed governor to adjust water flow to the runner in response to changing loads on the turbine , primarily to maintain operational stability. The reliability of these hydraulic systems is crucial for stable control of the unit, and minimizing the risks associated with mechanical failures of this primary regulating mechanism of the turbine. One proven way to enhance the performance and longevity of servomotors in hydropower plants is by using self-lubricating bushings in the mechanical connections and common wear points.
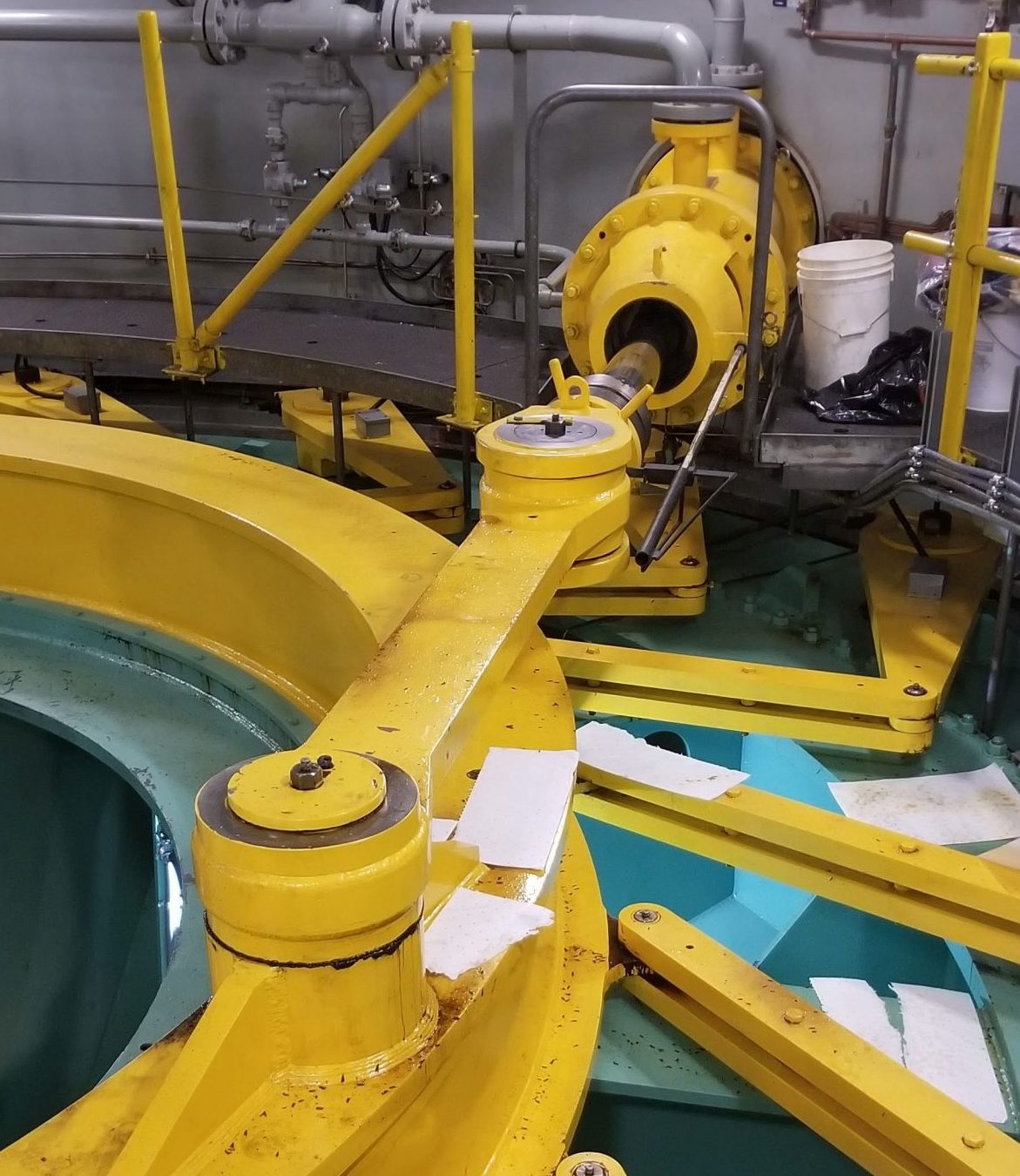
Servomotor Connected With Operating Ring (Grease Lubricated)
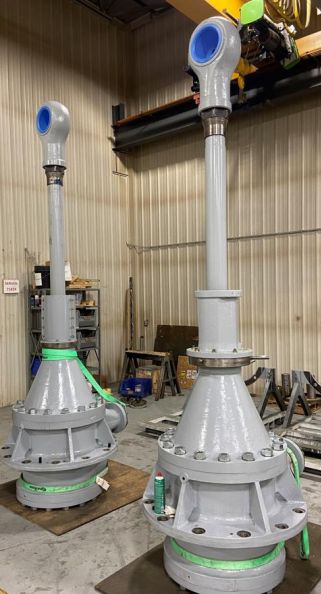
Newly Refurbished Servomotors
What’s Wrong With Greased Bushings?
Traditionally, servomotors were designed with bronze bushings, intended to be greased on a regular basis to ensure adequate lubrication to reduce friction and wear. If the greasing is not maintained, or misalignment of components causes edge loading and binding in the bronze bushings, this substantially increases the force required from the servo to move the wicket gates. As forces on the servo system increase, this in-turn will increase the wearing of all connected components and shorten their operational life. In the worst case, a seized servo bushing could prevent the servo from moving entirely, which would have severe consequences, potentially leading to loss of unit regulation and a runaway speed condition.
So Why Switch to Self-lubricated Bushings?
As in many other parts of the turbine (wicket gates, linkages, etc.), the use of self-lubricating bushings in the servomotors ensures low and stable friction, reduces wear and tear on components, and extends service life. Eliminating the need for periodic greasing and removal of old “auto-greasing” systems reduces maintenance costs and downtime, as well as improving the safety (reduced slip hazards) and general cleanliness around the servomotors. The absence of grease on the head-cover also reduces the risk of contamination of sump-pit water. By incorporating self-lubricating bushings into your servomotors, you can unlock the potential for improved performance, reliability, and longevity while minimizing the risks associated with seized bushings.
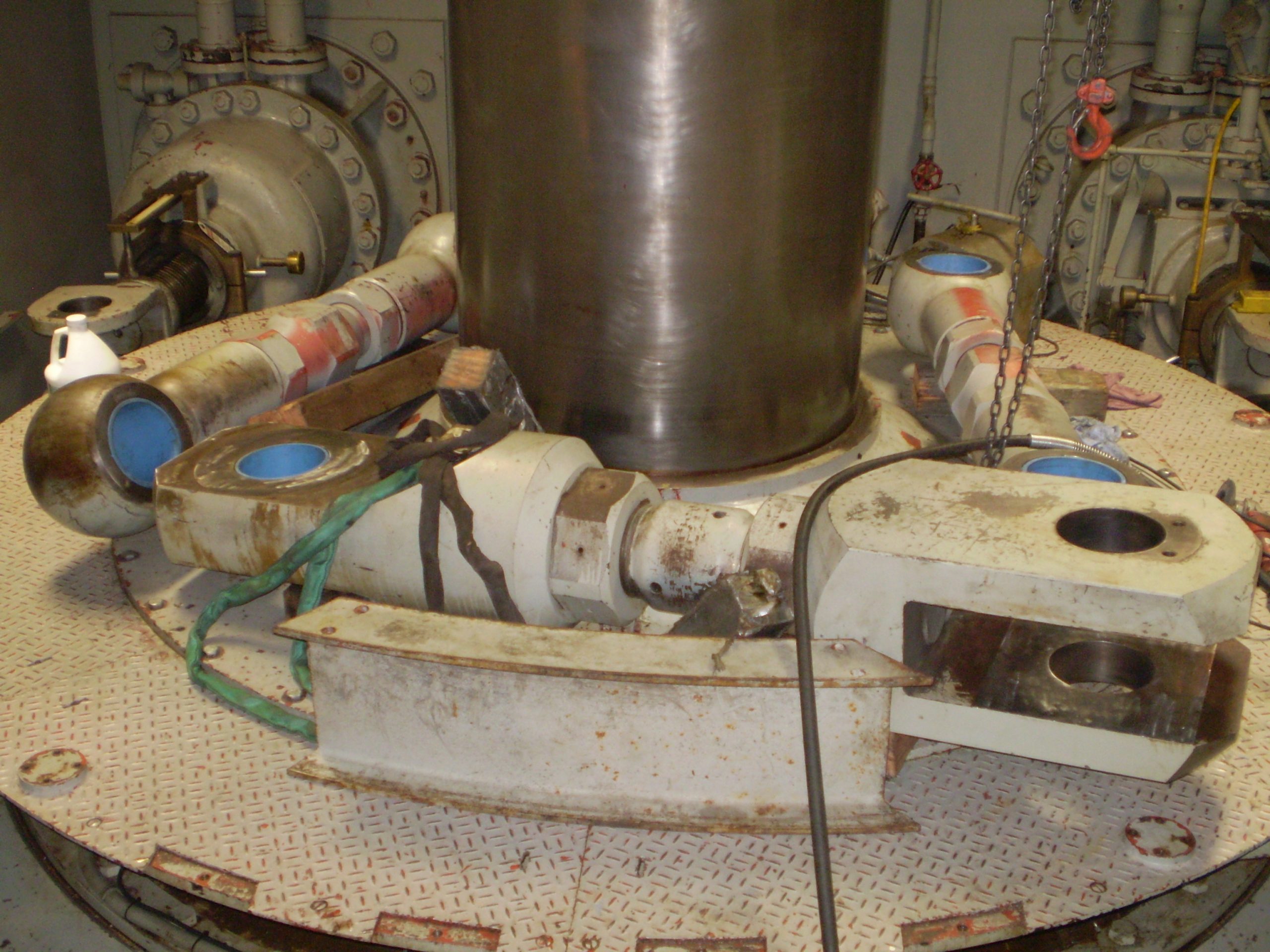
Grease-Free Servomotor Links, Ready for Assembly
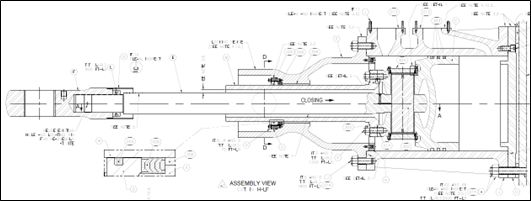
Typical Servomotor Cross-Section Drawing
Do you have challenges with your bearings, shaft seals, or water filtration systems and need a creative, cost-effective solution? Allow Millstream Engineering’s team of specialists to lead your group to a successful, economical solution. Contact us today.