Millstream in the Field – Paddling the Burnt River
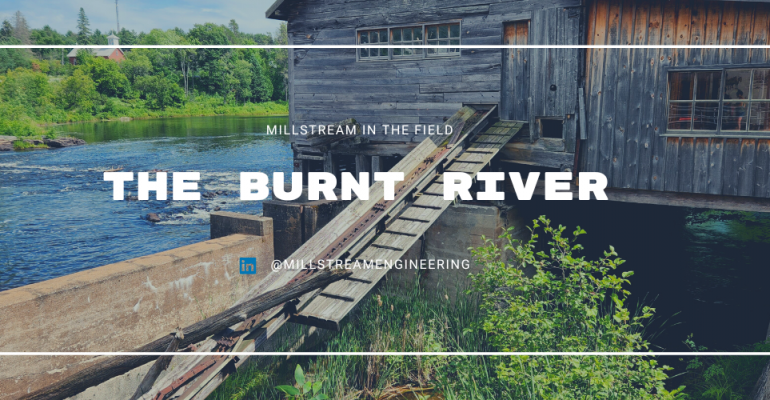
Millstream in the Field – Paddling the Burnt River
It was a beautiful weekend for a paddle, so it seemed like a good excuse to check out some of our historical waterways, and of course see if we could find some waterpower sites…
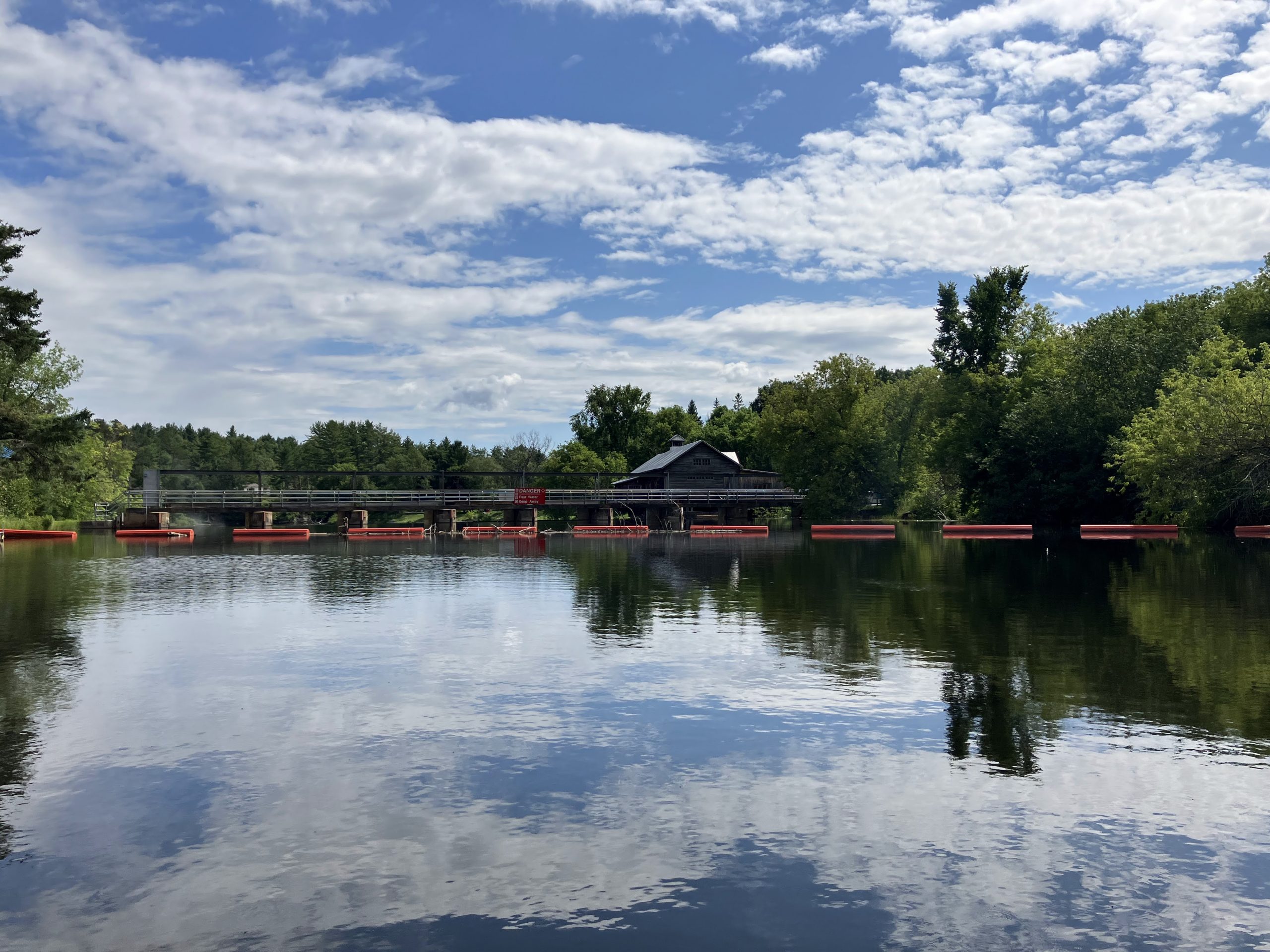
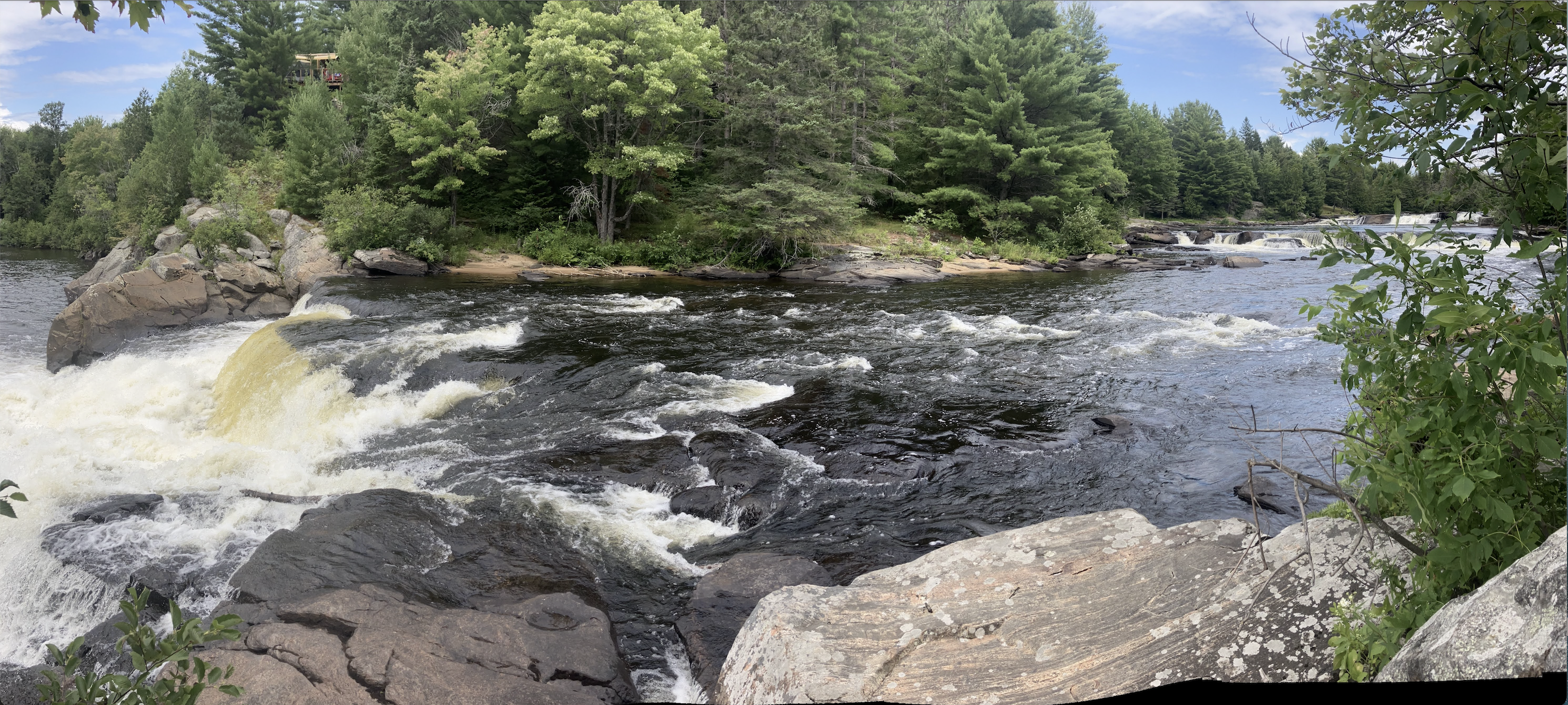
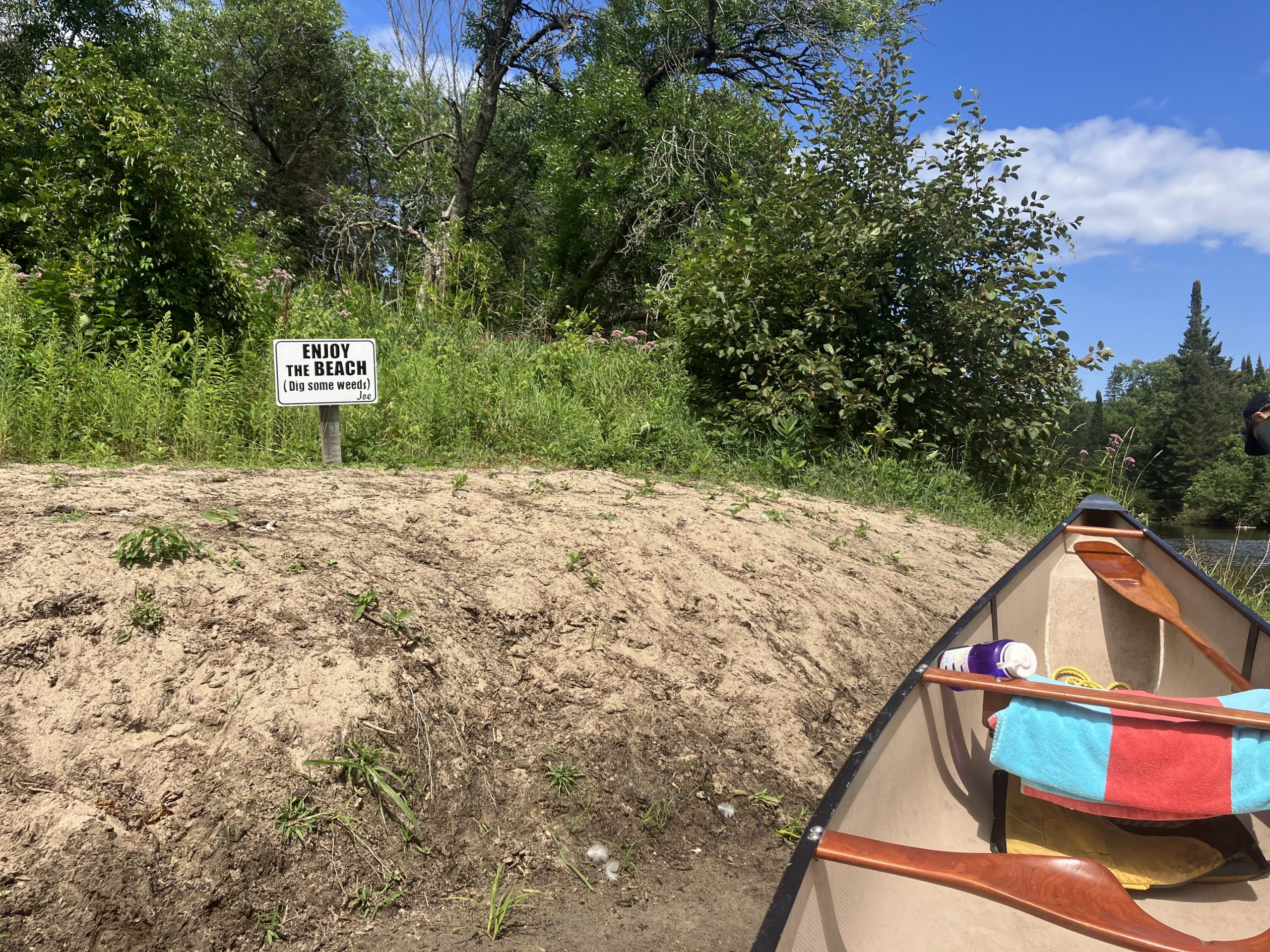
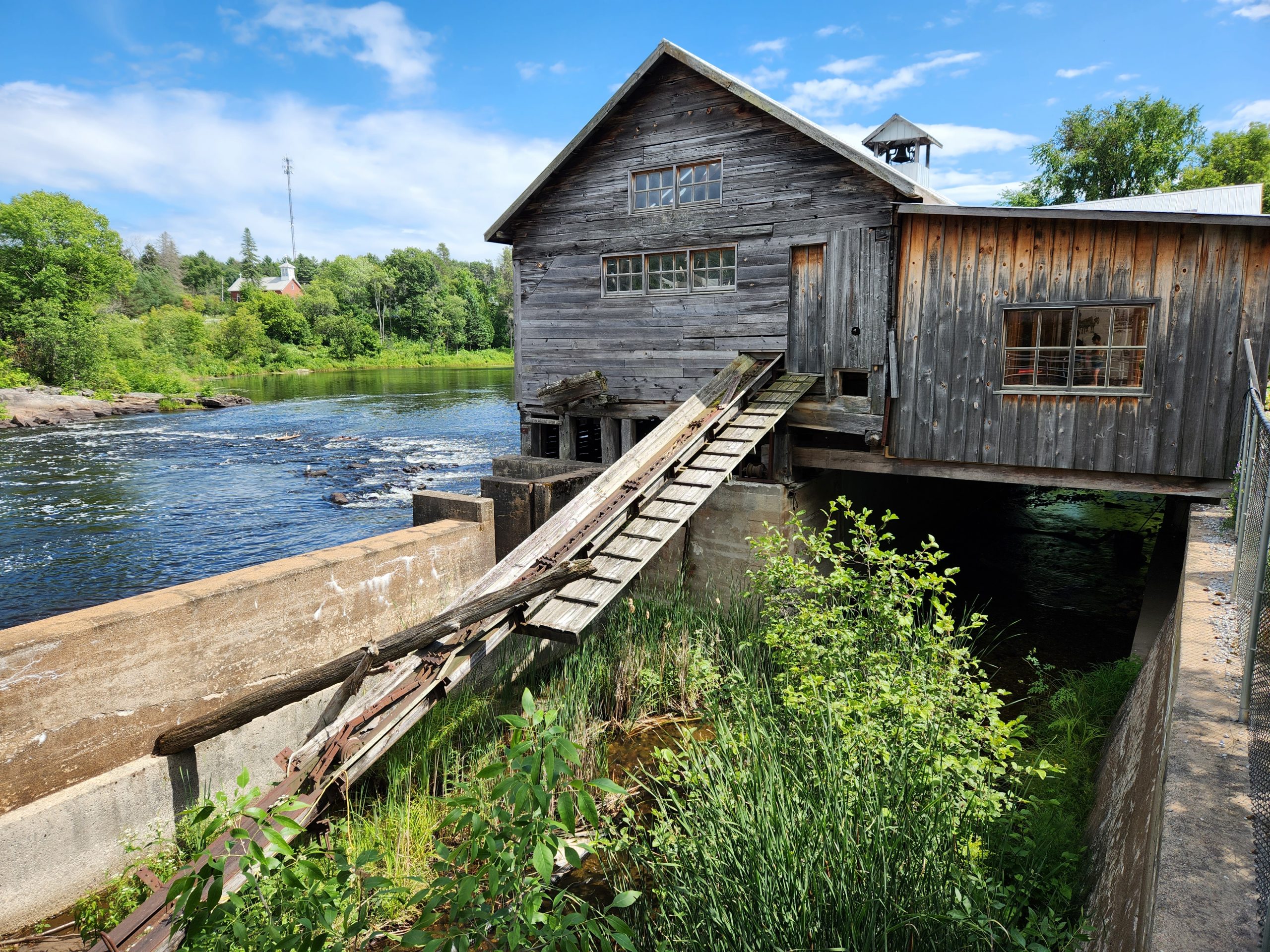
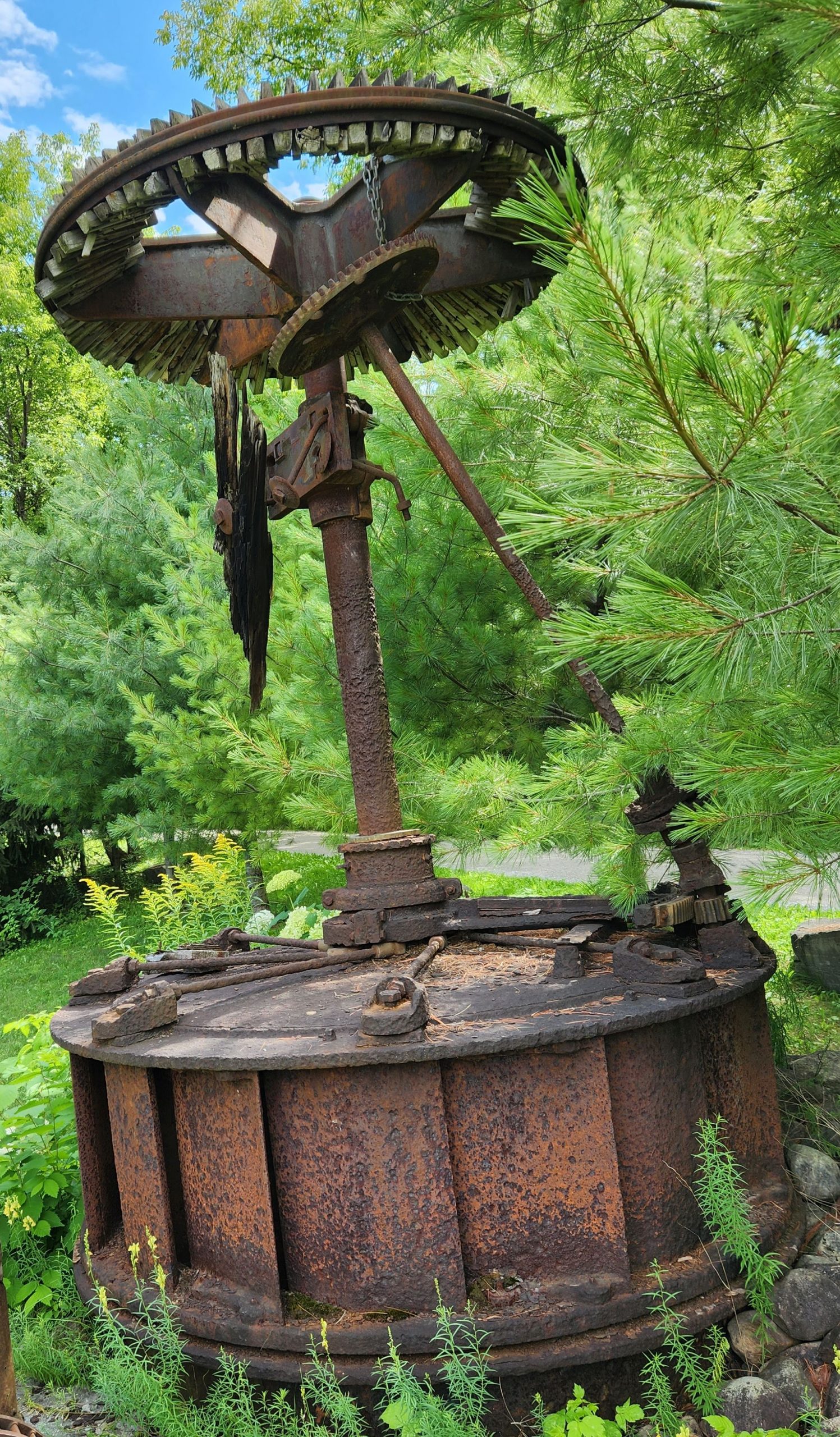
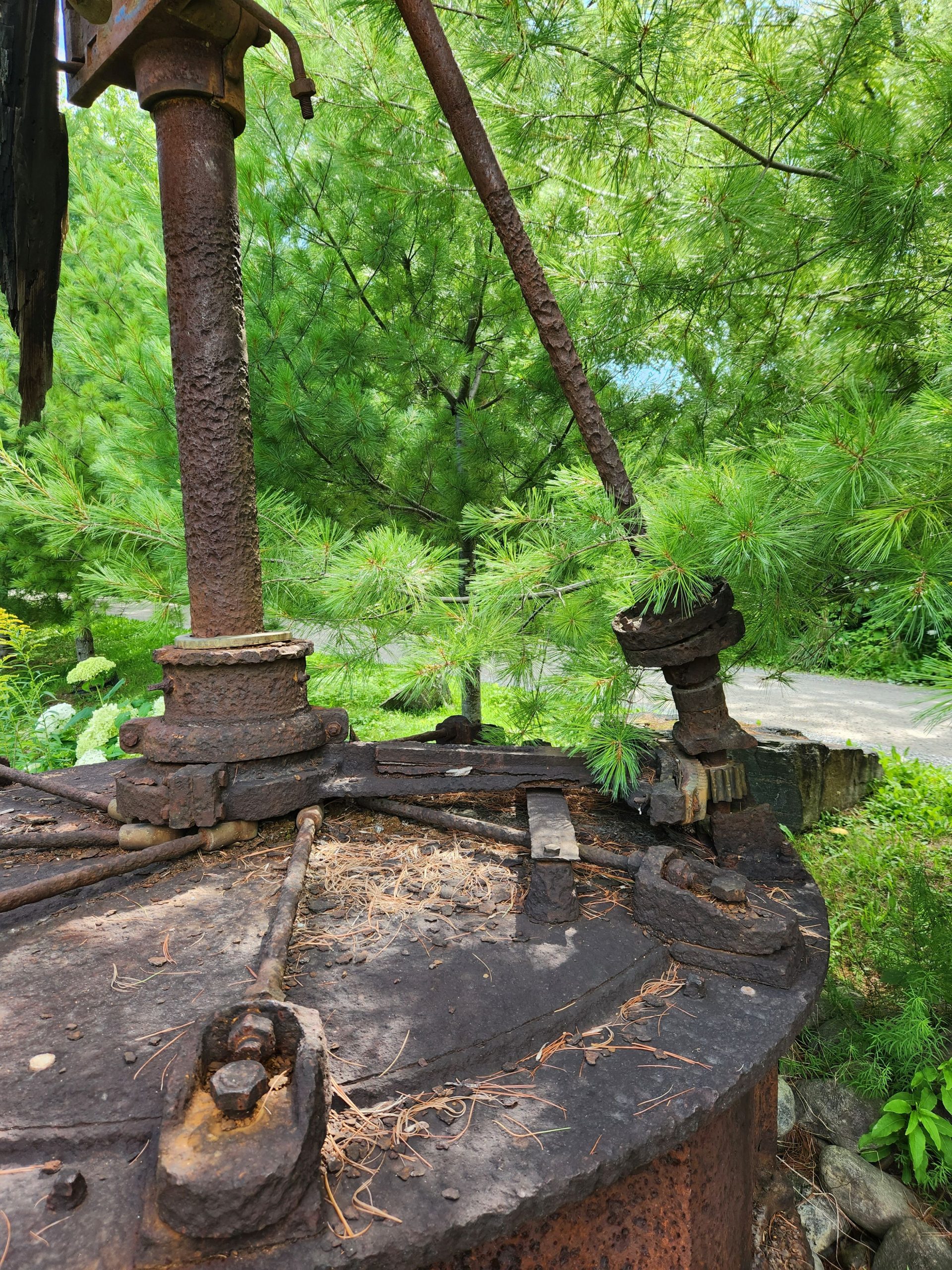
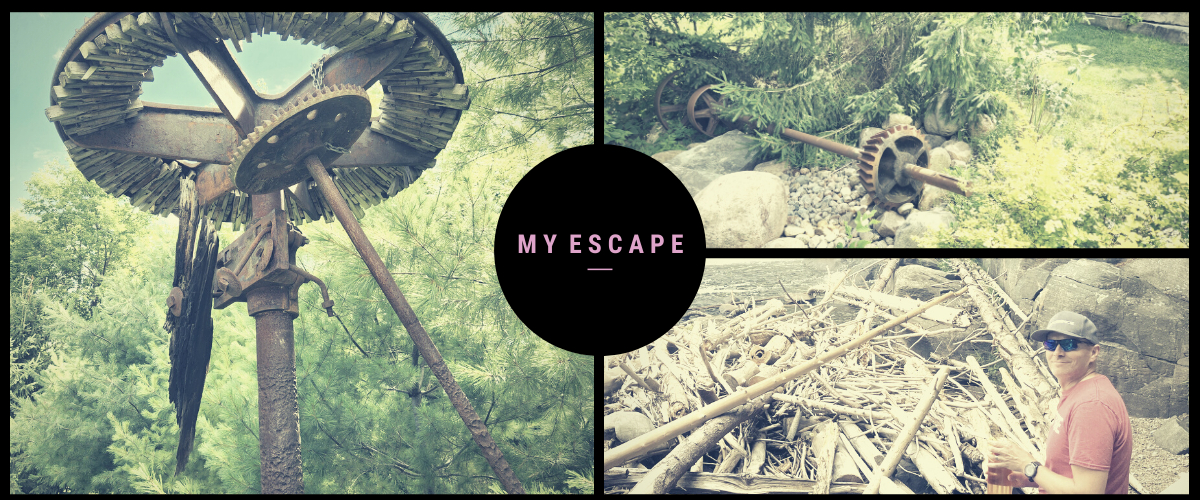